Possible cause/checklist:
- Position Linmot pusher plate:
Must be 1 mm behind tin plate edge!
- Adjust roller clearance on all 7 pairs according manual.
- First roller pair:
If you can’t get 0.1 mm roll clearance, check the toothed gears inside/outside. They may have a wrong lateral position; that ends in a too big clearance between the shafts!
- Test after setting:
Take off main and inner timing belt, rollers touching each other, all gears must have slight play!
- Check and adjust a well rollformed canbody:
Form of canbody must be round, both edges must have a parallel overlap, depending on the diameter!
– Diameter 52 mm = approx. 5 mm
– Diameter 99 mm = approx. 20 mm
- Check the feeder angle and rollformer speed according the recipe of the canbody you are currently running.
NOTE: «If parameter is different from recipe, it has been changed without authorization of Can Man! Any guarantee claims will be refused!»
- Check the curve you have in the tuning window with the recipe of the canbody you are currently running.
NOTE: «If parameter is different from recipe, it has been changed without authorization of Can Man! Any guarantee claims will be refused!»
- Make sure you have mounted the correct pair of final pusher fingers (see the diameter range engraved on the fingers).
- Check the actual overtravel with the help of the manual.
The recipe helps to adapt the speed of the incoming can into welding roller and the actual welding speed. In the best case, those speeds are equal.
Below you find a table of this recipe in steps of 10 mm can height.
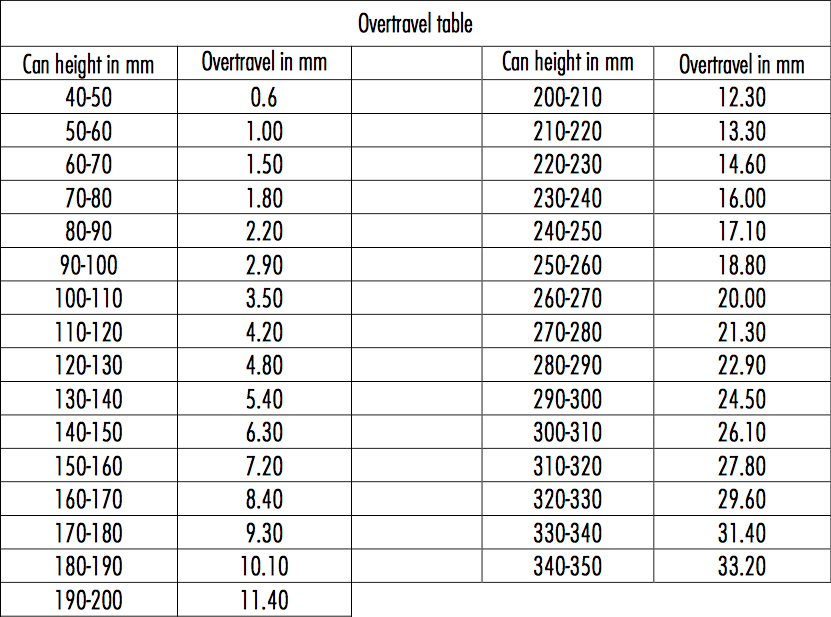
Turn the wheel of the synchrostar, that the pusher finger is as close as possible to the welding roll.
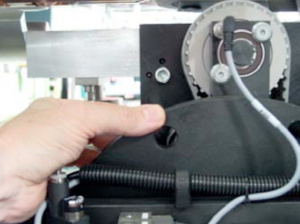
Measure now the distance from the top of the pusher finger to the center of the welding roll.
Distance = Can height – Overtravel Example:
Canheight: 122mm Overtravel: 4.8 mm
Distance: 117.2 mm
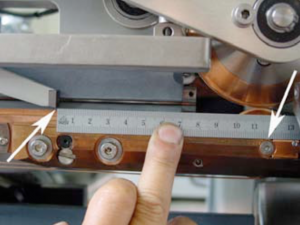