Possible reason:
- Check the blank cutting tolerances (can be supplied by Can Man): If the cutting tolerances are to big, the blanks will create all kind of downstacking errors.
- Check the burrs on the blank: If the burrs are to big, the blanks will create all kind of downstacking errors.
- Check the setting of the separating air: If the separating air is to low, the blanks can not being pulled down correctly. Try with more or less separating air.
- Clean the slider of the Linmot pusher according the manual.
- Magnets in the base plate might brake the blanks to much: Can Man does equip each base plate with 4 or max 6 magnets, depending on the the blank size. Remove eventually 2 magnets.
- Check the clearance of the first rollformer roller pair: The clearance between the lower and upper roller might be too small. Adjust the value according manual.
- Check the “Quick Change Level 40mm” setting acc. below pictures on the HMI: If the distance between the blank stack and the base plate measures 30 mm, set the function “Quick Change Level 40mm” to OFF. If you measure 40mm, set it to ON.
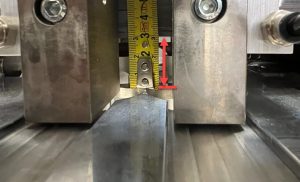
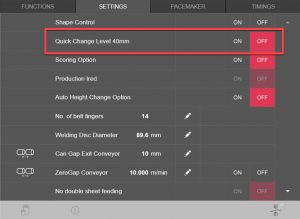
- Check the vacuum-stop point: The process to stop the vacuum must be activated by the mechanism around 3 mm before the blank arrives at the base plate. Please check the manual how to set.
- Check if the supporting air-pressure to stop the vacuum is adjusted correctly: Check the value / setting according the manual.
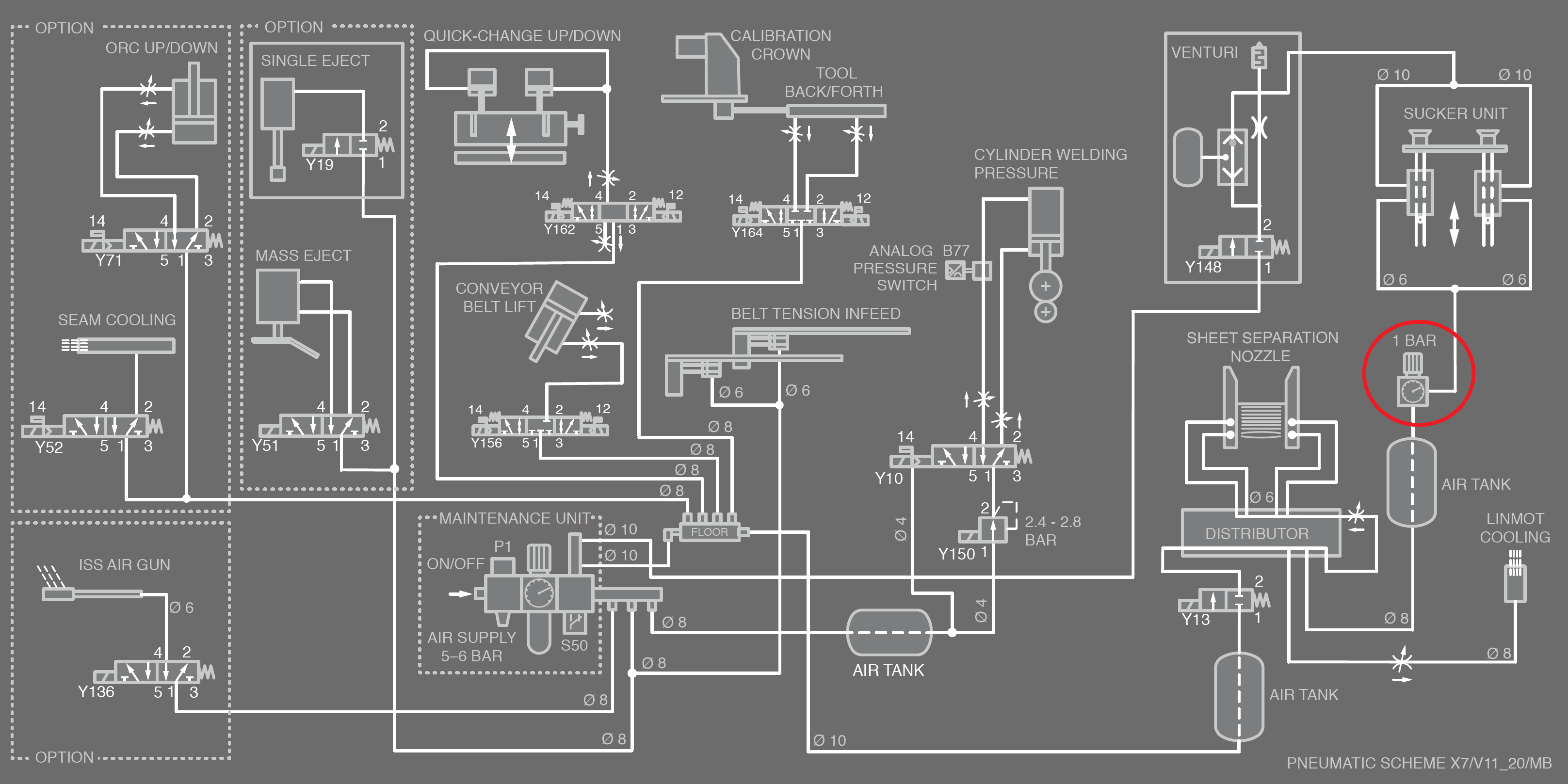